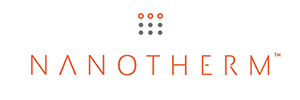
Tensile tester for PCB copper track 90 degree peel
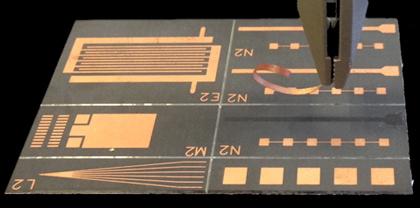
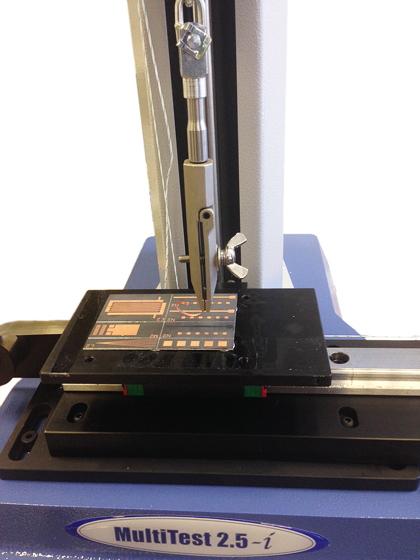
Solution
- MultiTest 2.5-i software-controlled foce test system
- Assisted pull peel table
Benefits
- Reliable and repeatable test routine
- Test to international standards
Having an in-house test capability is essential when developing new processes and products. Having the Mecmesin tester at Cambridge Nanotherm has allowed us to reduce test cycles significantly. The software package also gives us the ability to analyse the subtle differences in adhesion mechanisms and also gives us the ability to produce detailed reports for our suppliers and customers.
Steven Curtis, Chief Engineering Officer
Cambridge Nanotherm Ltd
Requirement
Cambridge Nanotherm Ltd produce a unique, technologically-advanced substrate for the thermal management of electronic components. Their patented Nanotherm™ technology creates a nano-ceramic dielectric layer on the surface of an aluminium substrate onto which a circuit layer is formed.
Metal-backed printed circuit board (MBPCB) products utilise this process to provide an industry-leading low thermal resistance and the ability to significantly reduce component operating temperature.
The conductive copper bonded to the ceramic layer is able to be patterned with standard techniques, allowing customer designs to be readily manufactured.
The adhesion of the tracks to the substrate is a key property of the material and this peel strength is tested according to Institute of Printed Circuits IPC-TM-650 test standards.
In order to continue to pass these industry tests and further enhance the capability to develop high quality, innovative products, the company required a solution to test in-house, to replace the existing out-sourced testing.
Solutions
Mecmesin supplied a single column computer-controlled test stand complete with an assisted-pull peel table to accurately control the constant 90 degree peel angle. Having previously performed the tests with other equipment, the company were able to calibrate existing data against that acquired from demonstrations, to verify accuracy and evaluate the full process for suitability.
Lightweight pinch grips hold the thin sample securely across its full width, but avoid breakage, while the clevis chain link, in conjunction with the horizontally driven table, ensures the crosshead’s vertical travel resolves to a 90 degree peel without jarring or adding noise to the measurement.
The peel is performed at a constant 2”/min and the salient force value is the calculated average minimum. Emperor™ software controls the whole process and the programming flexibility will allow the company to develop further tests, if required, to ensure quality assurance for these cutting-edge technologies.
This in-house capability also enables quicker optimisation within design cycles and eliminates the costs incurred for
Test equipment
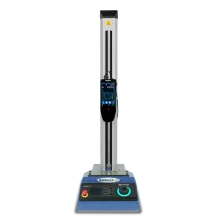
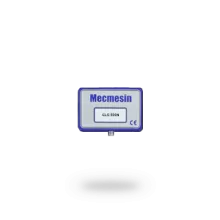
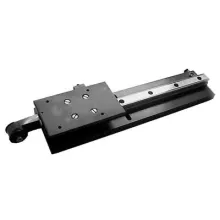
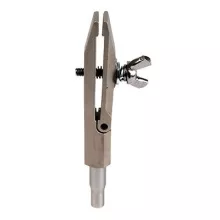